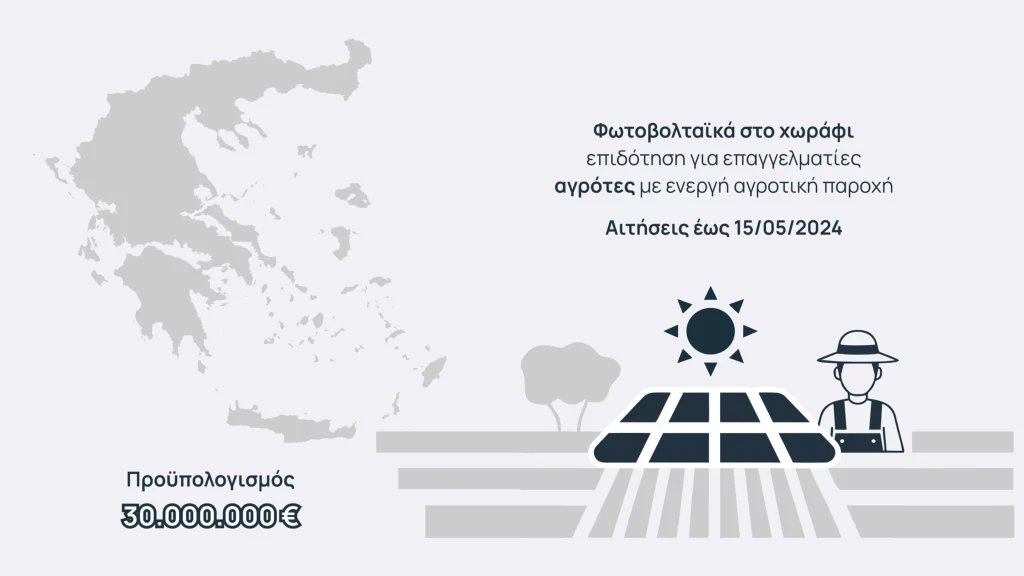
The implementation of a quality management system in one company inspires confidence in the customer, the market, the employees and, in general, lends validity and reliability. The main benefits arising for the companies from the application of the ISO standards relating to the following:
– To improve the public image of the company
– Increased customer satisfaction
– Minimize λαθώ
– Improve process controls
– Use the template as a means of promotion and marketing
– Penetration of the global market and increasing exports
– Minimizing of fines – compliance with legislation
– Increased awareness of the company's employees in matters of safety
– Protection of the environment
The implementation of a quality system for a company involves a number of stages which, of course, there are variations depending on the object of the operation, the size, and other factors. However, the general steps are:
Step 1: Fix – Evaluation of the current status
– Detailed mapping of the existing mode of operation and to identify deviations from the norm.
– Given the guidelines, made suggestions for improvement.
– Set out a detailed timetable for the development and implementation of the system.
Stage 2: Design And Development Of A Quality Management System
– It is formed of the Quality Manual in which there is an analytical description of the system.
– Mapping of the individual processes in a way that is clear and detailed.
– Information and training of personnel.
– Design the required forms and documents.
Stage 3: Support the implementation of a quality system: Conduct internal audits – Review system
– Regular checks are carried out for the monitoring of the project and the satisfactory operation of the parts.
– Made evidence-based interventions or reforms (depending on the findings of the controls) with the aim of better organization.
– A report shall be submitted with the audit findings.
Stage 4: Certification of a Quality Management System by an accredited certification body
– Preparation of an application for assessment to the Certification Body.
– Inspection of the system by the accredited body.
– Remove any comments/non-conformities, corrective actions (if required).
– Download A Certificate Of Quality.
In ΙΩΝΙΚΗ we have the necessary experience and expertise to fully support the design and implementation of a quality system for your business.
For more information, request a telephone appointment by pressing the button below, and a qualified economist of our company will contact you.