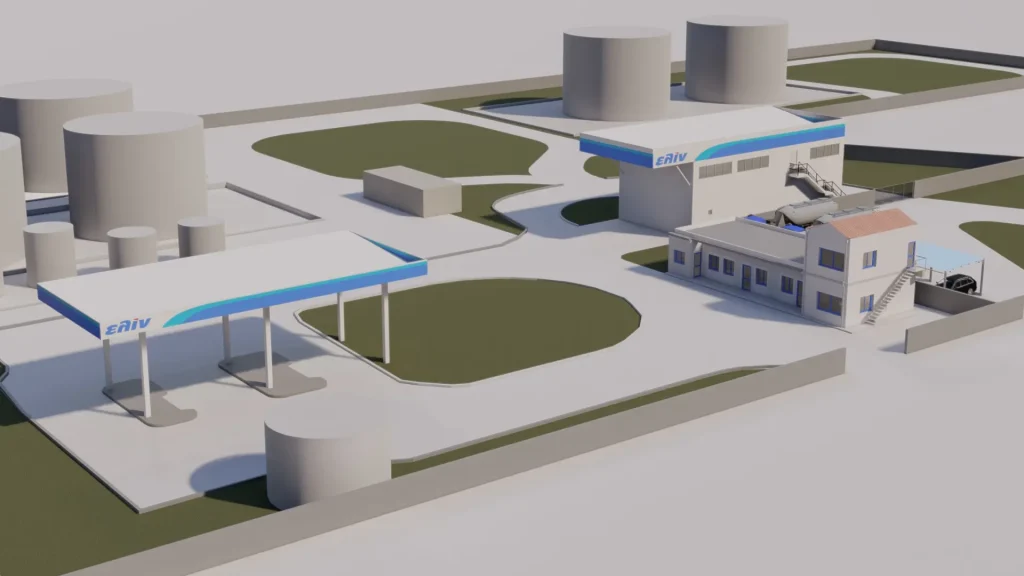
Industry 4.0, also known as the Fourth Industrial Revolution, is bringing rapid changes to the way factories operate and how goods are produced.
The integration of advanced technologies such as the Internet of Things (IoT), artificial intelligence (AI), and cloud computing leads to the creation of smart factories that can adapt to changing market conditions and customer demands, resulting in improved efficiency, performance, and flexibility. However, is this evolution a necessity or a luxury for the industry?
Historical Overview: The Evolution from the 18th Century to Today
The First Industrial Revolution (Industry 1.0) began in the late 18th century and was characterized by the use of steam to power machines in textiles and other manufacturing facilities. During this period, we witnessed the first significant increase in the mass production of goods.
At the end of the 19th century, we entered the era of the Second Industrial Revolution (Industry 2.0), where the use of electricity and the assembly line for operating machines in factories distinguished this period. This led to further increases in productivity and mass production of goods on an even larger scale.
Industry 3.0 (Third Industrial Revolution) began in the mid-20th century and was characterized by the use of computers and automation in manufacturing, through which programmable machines and robots were developed, thereby increasing accuracy in production processes.
The accuracy in production processes was the defining difference between the third and the first two industrial revolutions. There is an evolution primarily due to technology that has brought us to Industry 4.0 today, where, in addition to increasing production, which was the main goal of the first two industrial revolutions, smart factories now focus on information and knowledge, which are stored in the cloud, ultimately aiming for better decision-making and replacing harmful jobs with robotic arms.
Productivity Increase of Up to 30% with Internet of Things and Artificial Intelligence
One of the main drivers of Industry 4.0 is IoT, which enables the connection of machines, devices, and sensors to the internet, allowing them to communicate with each other and share data.
This enables real-time monitoring and control of production processes, as well as the ability to predict and prevent equipment failures.
The use of IoT in manufacturing can increase productivity by up to 30%, according to a study by McKinsey. It also allows manufacturers to respond quickly to changes in demand, reducing the risk of overproduction and resource waste.
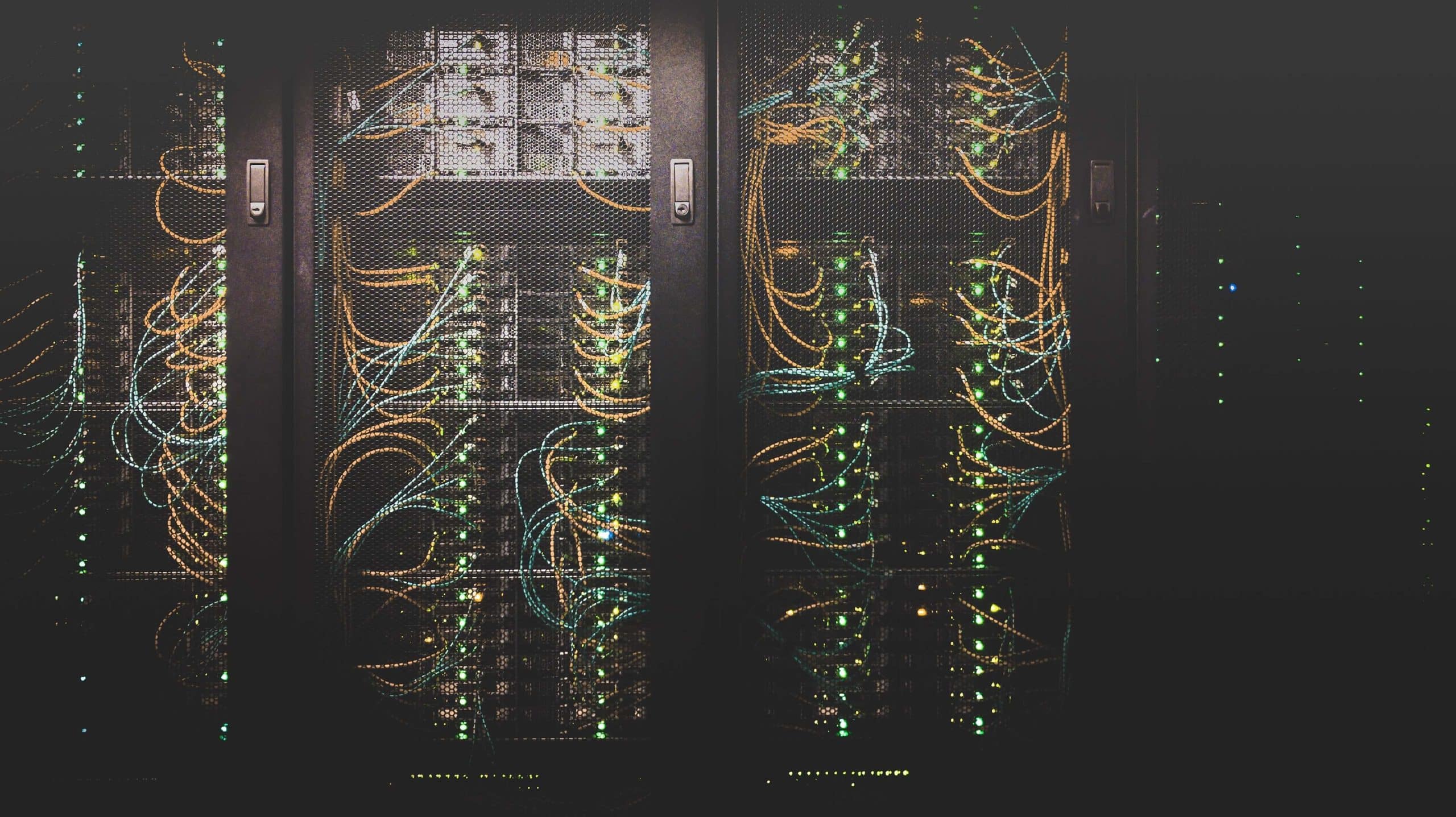
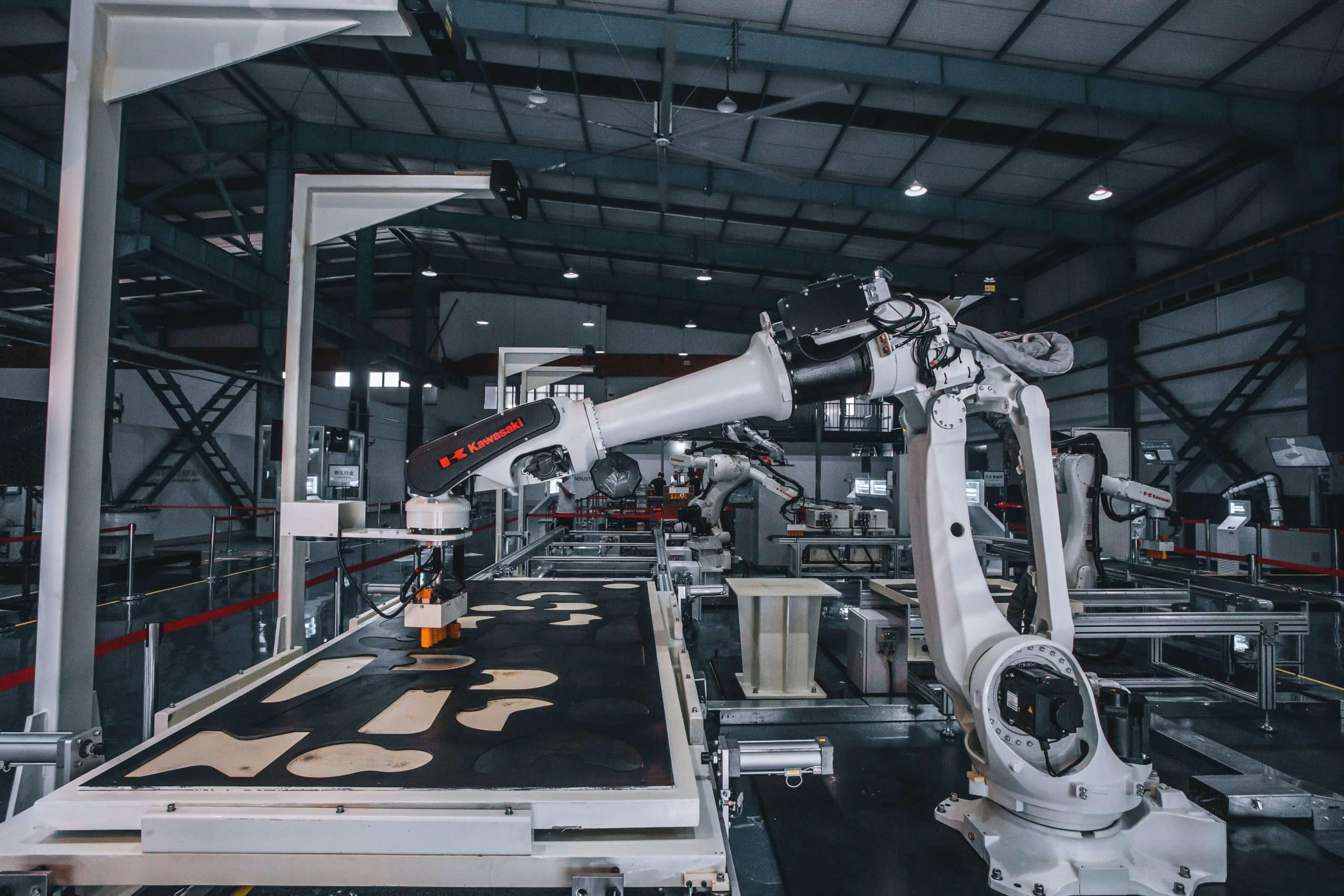
Artificial intelligence also plays a significant role in Industry 4.0, using machine learning algorithms to analyze data from IoT devices and make predictions about future performance.
This enables the optimization of production processes and the identification of new business opportunities. For example, AI-powered robots can be used to perform repetitive tasks, freeing human workers to focus on more complex and value-added activities.
Furthermore, AI can be utilized to improve product quality by identifying and correcting defects in real time.
Analysis of Large Volumes of Data Stored in the Cloud, Leads to Better Business Decisions
Cloud computing is also a crucial aspect of Industry 4.0, as it allows for the storage and analysis of large amounts of data from IoT devices and other sources. This enables manufacturers to make better decisions and improve their operations.
Additionally, cloud computing provides manufacturers access to advanced analytical tools and applications, which can provide insights into production processes and enhance efficiency.
Industry 4.0 has all the necessary infrastructure to radically change the management of the supply chain, improving traceability and visibility, enabling manufacturers to respond more quickly to disruptions and reducing the risk of inventory depletion.
Technologies like 3D printing and advanced robotics allow manufacturers to produce products with greater flexibility and customization, resulting in better responses to customer needs.
Data Security Raises Concerns for Industry 4.0
Despite the benefits, Industry 4.0 also raises concerns about data privacy and security, as well as the impact on jobs as automation and the use of artificial intelligence increase.
Companies must ensure that their data is protected and that they comply with relevant regulations, such as the General Data Protection Regulation (GDPR) in Europe.
Companies should also consider how to reskill their workforce to adapt to the new technological landscape.
However, the need for Industry 4.0 is not only about keeping industries competitive but is a necessity for their survival in the sector.
The global economy is continuously changing at a rapid pace, and manufacturers must be able to adapt to changing market conditions and customer demands.
Industry 4.0 technologies contribute to these developments by increasing efficiency, reducing costs, and improving product quality.
Industry 4.0 helps manufacturers create new products and services as well as develop new business models.
Industry 4.0: Evolution and Necessity Simultaneously
In summary, Industry 4.0 is not only an evolution but also a necessity for manufacturers to remain competitive and survive in the global market while providing greater security for the workforce.
The cloud infrastructure has been around for many years, in contrast to automated processes, digital controls, and the use of robotic arms, which are experiencing an explosion of development.
The Fourth Industrial Revolution has just begun.
Industry 4.0: Evolution or Necessity?
ΙΩΝΙΚΗ Engineering
Industry 4.0, also known as the Fourth Industrial Revolution, is bringing rapid changes to the way factories operate and how goods are produced.
The integration of advanced technologies such as the Internet of Things (IoT), artificial intelligence (AI), and cloud computing leads to the creation of smart factories that can adapt to changing market conditions and customer demands, resulting in improved efficiency, performance, and flexibility. However, is this evolution a necessity or a luxury for the industry?
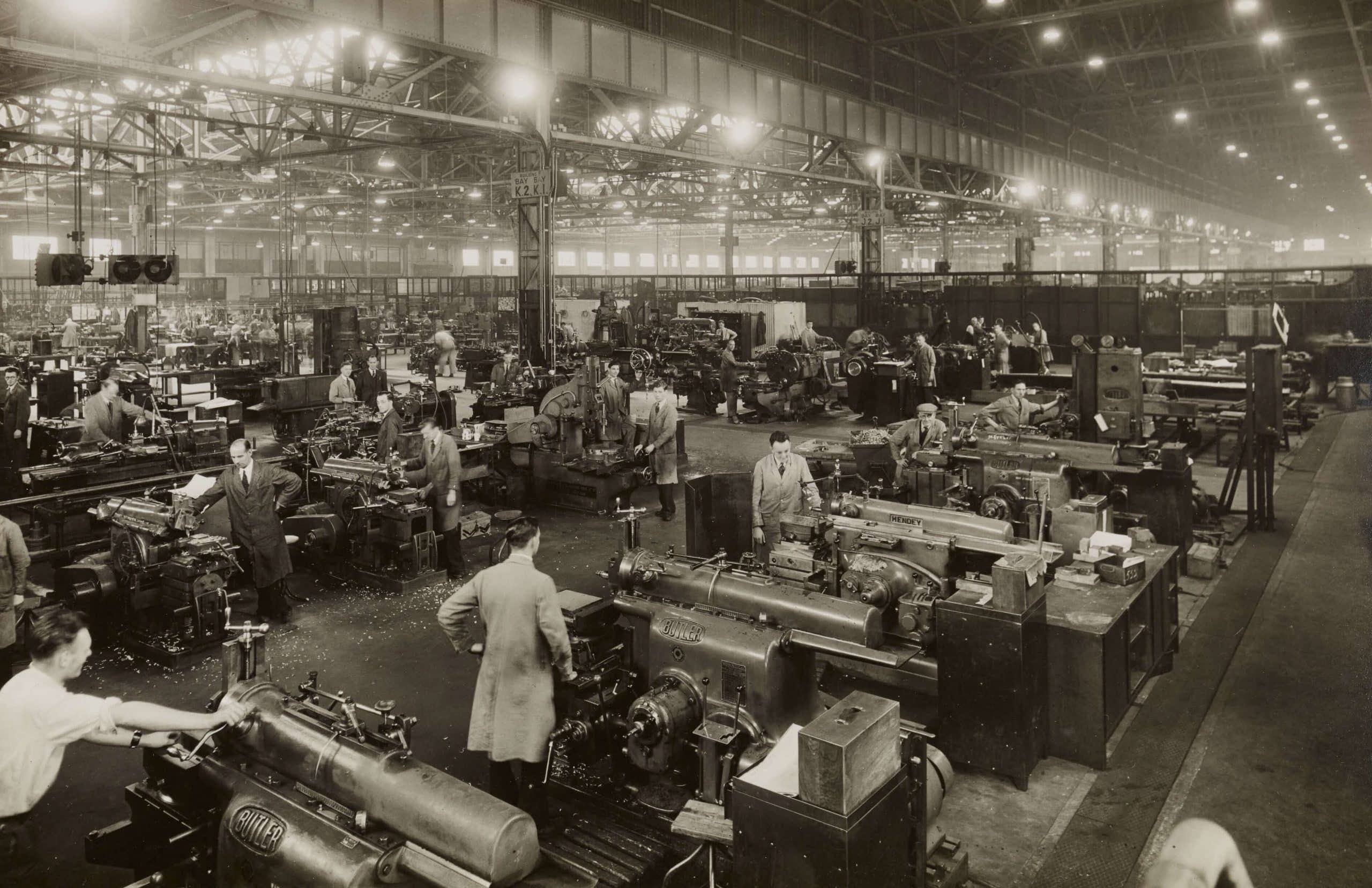
Historical Overview: The Evolution from the 18th Century to Today
The First Industrial Revolution (Industry 1.0) began in the late 18th century and was characterized by the use of steam to power machines in textiles and other manufacturing facilities. During this period, we witnessed the first significant increase in the mass production of goods.
At the end of the 19th century, we entered the era of the Second Industrial Revolution (Industry 2.0), where the use of electricity and the assembly line for operating machines in factories distinguished this period. This led to further increases in productivity and mass production of goods on an even larger scale.
Industry 3.0 (Third Industrial Revolution) began in the mid-20th century and was characterized by the use of computers and automation in manufacturing, through which programmable machines and robots were developed, thereby increasing accuracy in production processes.
The accuracy in production processes was the defining difference between the third and the first two industrial revolutions. There is an evolution primarily due to technology that has brought us to Industry 4.0 today, where, in addition to increasing production, which was the main goal of the first two industrial revolutions, smart factories now focus on information and knowledge, which are stored in the cloud, ultimately aiming for better decision-making and replacing harmful jobs with robotic arms.
Productivity Increase of Up to 30% with Internet of Things and Artificial Intelligence
One of the main drivers of Industry 4.0 is IoT, which enables the connection of machines, devices, and sensors to the internet, allowing them to communicate with each other and share data.
This enables real-time monitoring and control of production processes, as well as the ability to predict and prevent equipment failures.
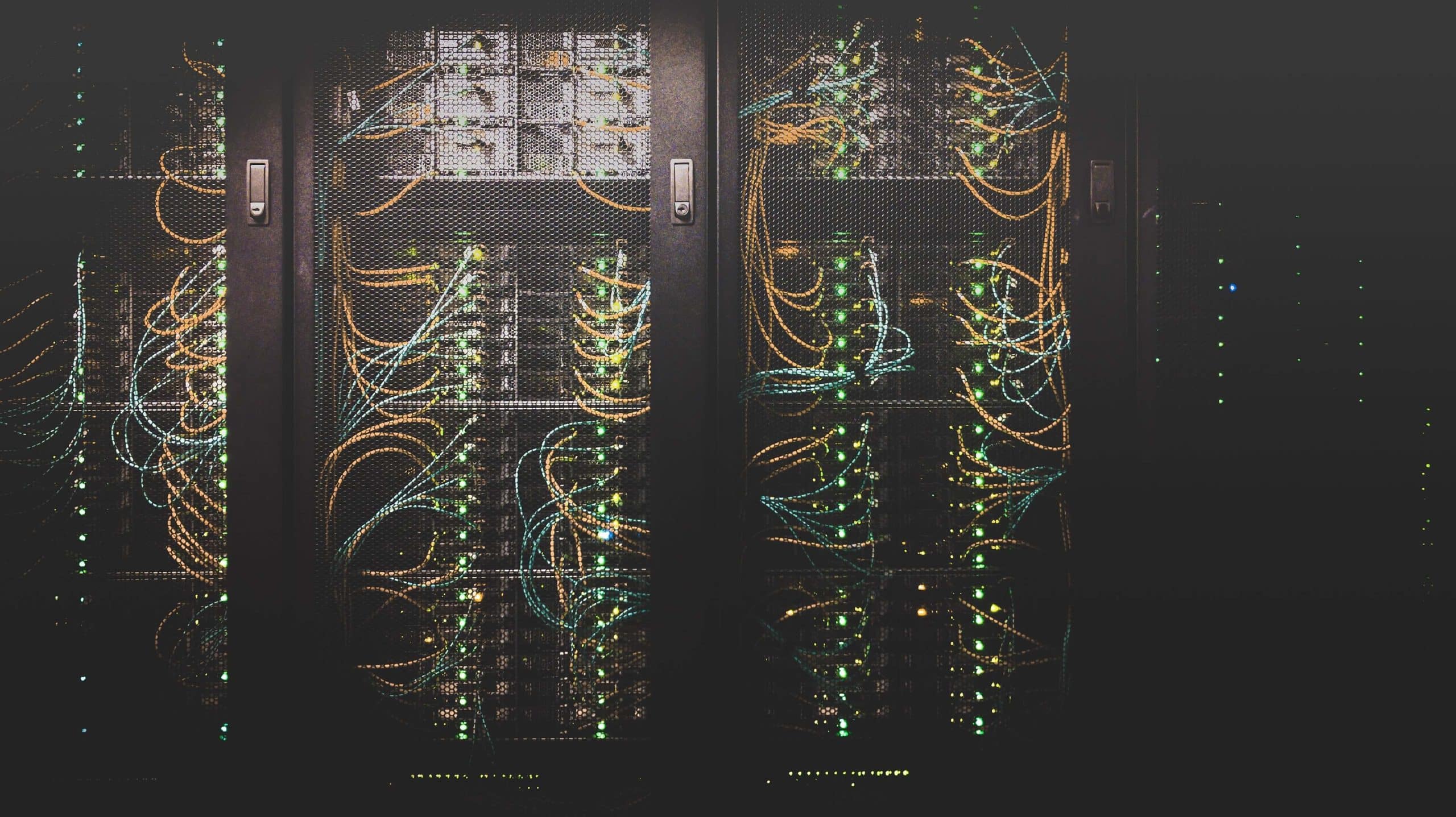
The use of IoT in manufacturing can increase productivity by up to 30%, according to a study by McKinsey. It also allows manufacturers to respond quickly to changes in demand, reducing the risk of overproduction and resource waste.
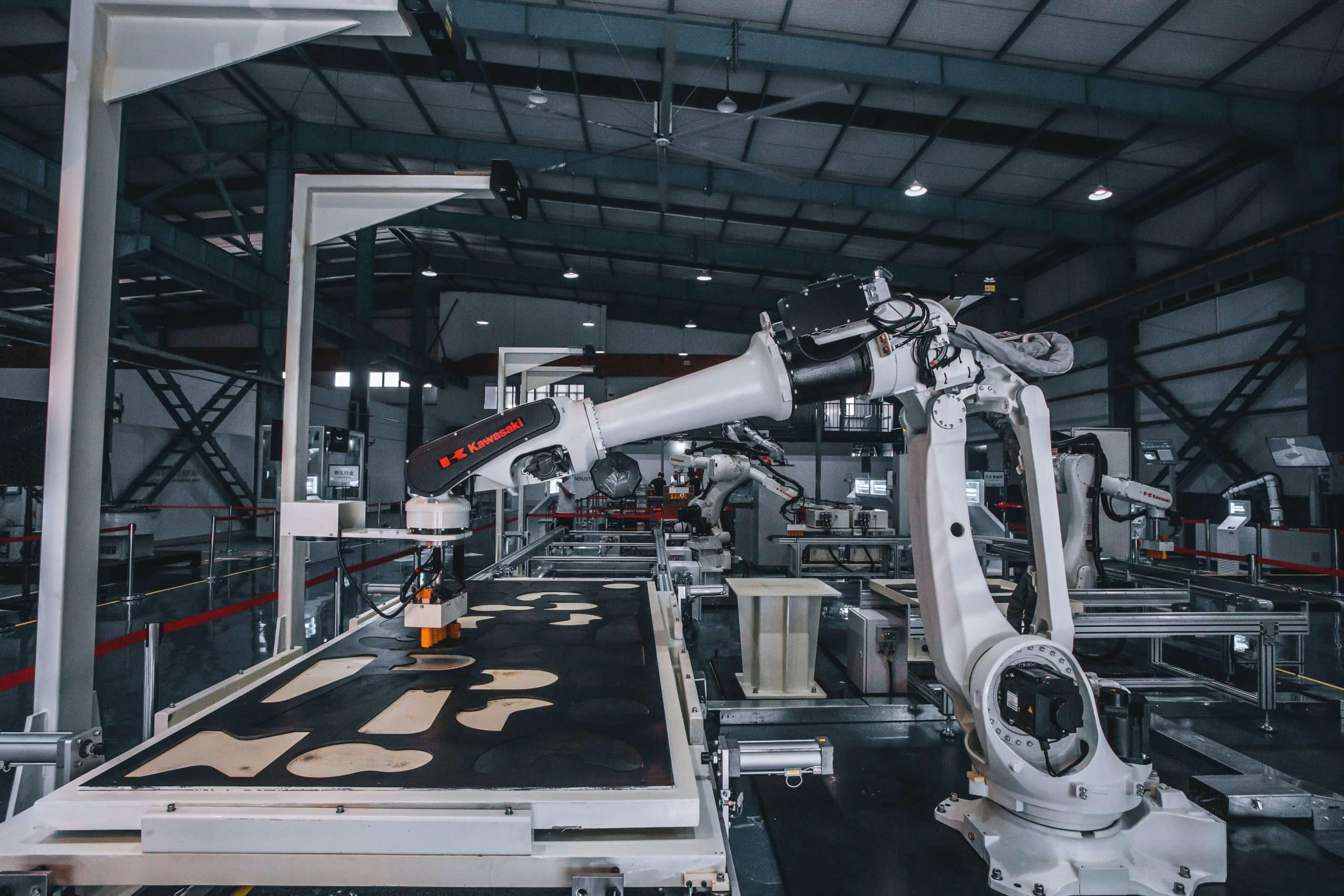
Artificial intelligence also plays a significant role in Industry 4.0, using machine learning algorithms to analyze data from IoT devices and make predictions about future performance.
This enables the optimization of production processes and the identification of new business opportunities. For example, AI-powered robots can be used to perform repetitive tasks, freeing human workers to focus on more complex and value-added activities.
Furthermore, AI can be utilized to improve product quality by identifying and correcting defects in real time.
Analysis of Large Volumes of Data Stored in the Cloud, Leads to Better Business Decisions
Cloud computing is also a crucial aspect of Industry 4.0, as it allows for the storage and analysis of large amounts of data from IoT devices and other sources. This enables manufacturers to make better decisions and improve their operations.
Additionally, cloud computing provides manufacturers access to advanced analytical tools and applications, which can provide insights into production processes and enhance efficiency.
Industry 4.0 has all the necessary infrastructure to radically change the management of the supply chain, improving traceability and visibility, enabling manufacturers to respond more quickly to disruptions and reducing the risk of inventory depletion.
Technologies like 3D printing and advanced robotics allow manufacturers to produce products with greater flexibility and customization, resulting in better responses to customer needs.
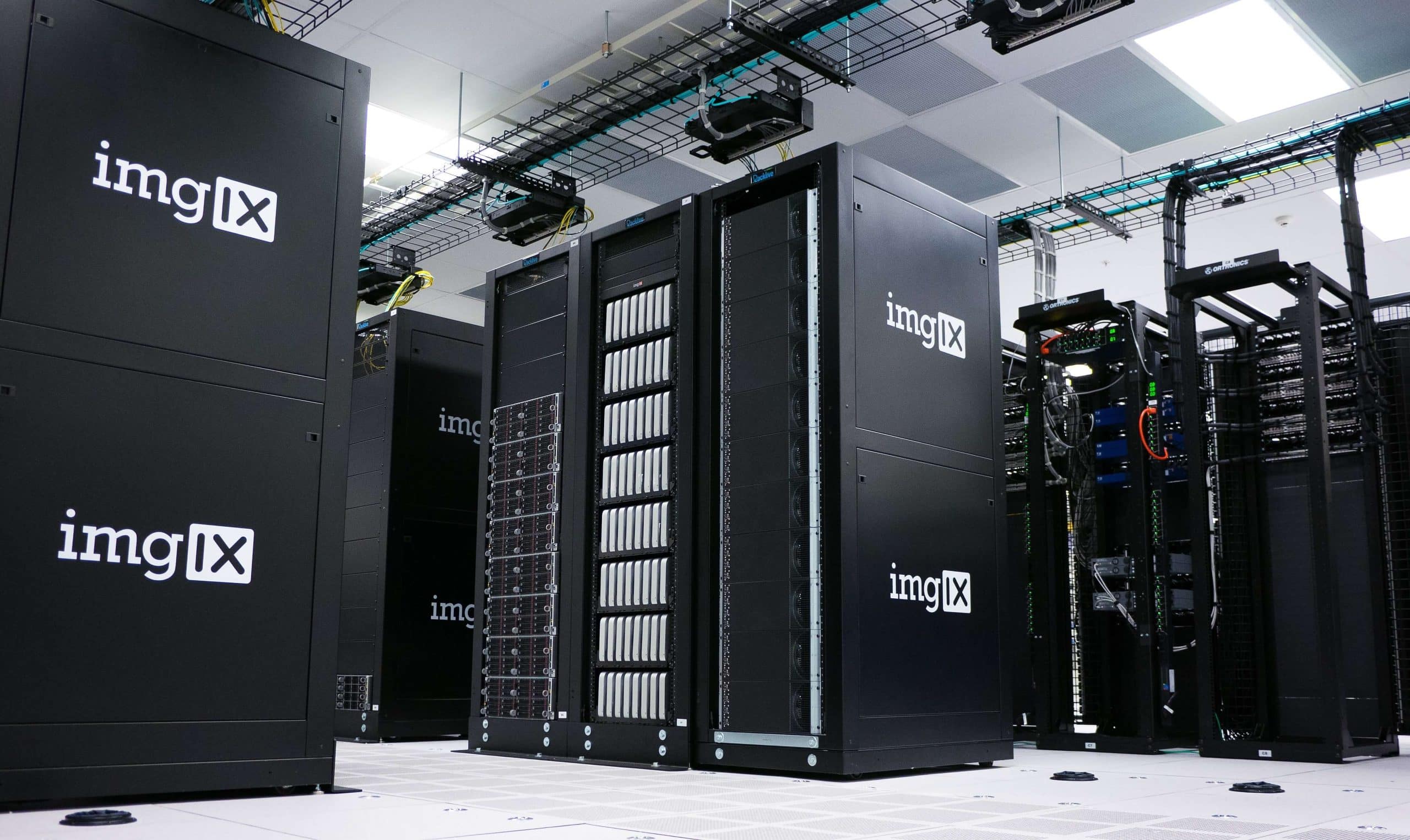
Data Security Raises Concerns for Industry 4.0
Despite the benefits, Industry 4.0 also raises concerns about data privacy and security, as well as the impact on jobs as automation and the use of artificial intelligence increase.
Companies must ensure that their data is protected and that they comply with relevant regulations, such as the General Data Protection Regulation (GDPR) in Europe.
Companies should also consider how to reskill their workforce to adapt to the new technological landscape.
However, the need for Industry 4.0 is not only about keeping industries competitive but is a necessity for their survival in the sector.
The global economy is continuously changing at a rapid pace, and manufacturers must be able to adapt to changing market conditions and customer demands.
Industry 4.0 technologies contribute to these developments by increasing efficiency, reducing costs, and improving product quality.
Industry 4.0 helps manufacturers create new products and services as well as develop new business models.
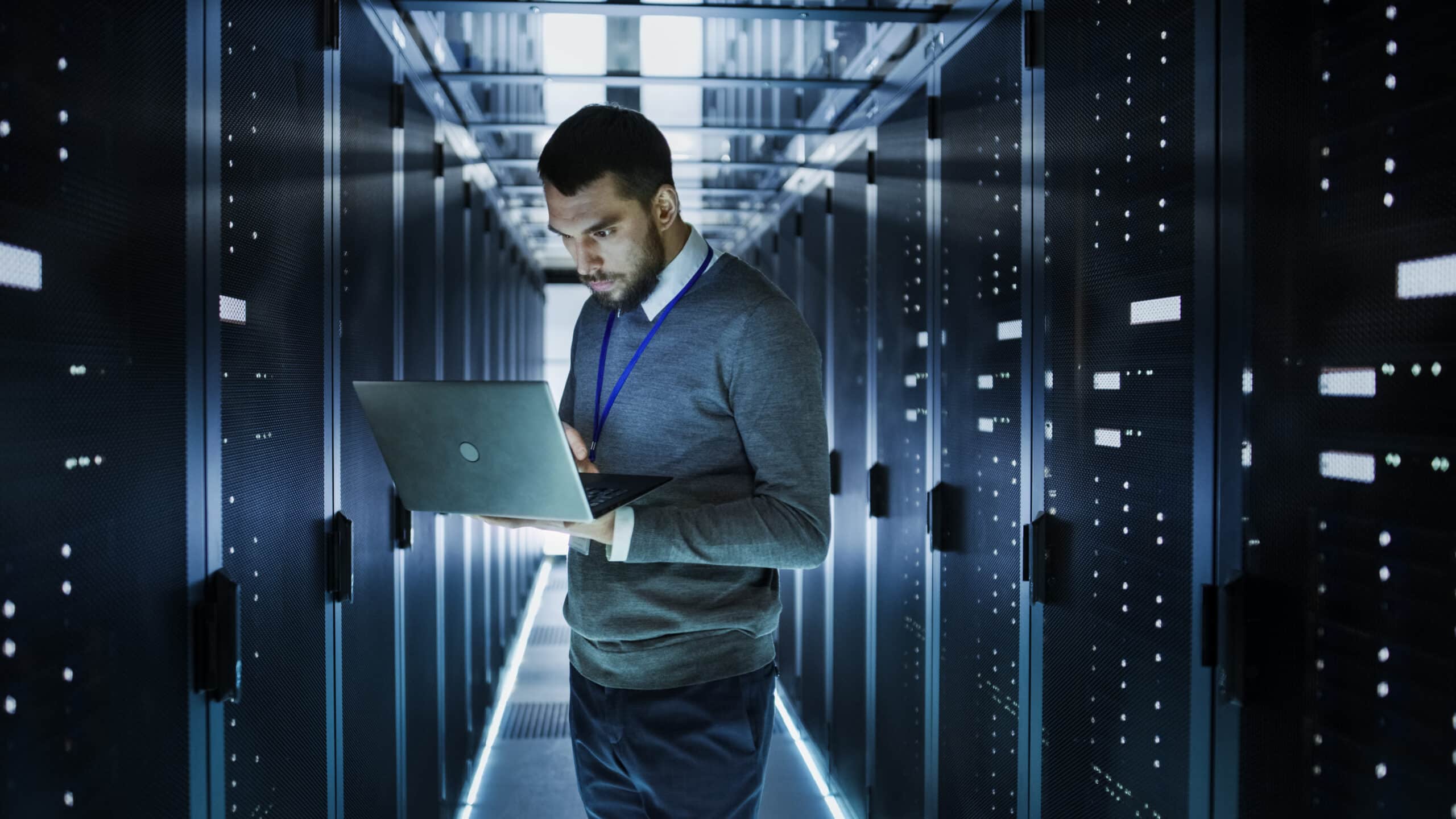
Industry 4.0: Evolution and Necessity Simultaneously
In summary, Industry 4.0 is not only an evolution but also a necessity for manufacturers to remain competitive and survive in the global market while providing greater security for the workforce.
The cloud infrastructure has been around for many years, in contrast to automated processes, digital controls, and the use of robotic arms, which are experiencing an explosion of development.
The Fourth Industrial Revolution has just begun.